Arcos develops and implements automatic finishing systems with the use of robots and cutting-edge technologies. Arcos robotic cells guarantee great reliability and flexibility: their technology, in fact, guarantees the highest level of performance for multiple and diversified processes (from the handling of objects, assembly, quality control, sorting, painting, etc.).
All robotic finishing systems are designed and built to meet the production needs of the customer, for this reason one of their strengths is the possibility of including a fully customized robotic cell in your production system. The close collaboration with Arcos engineers and designers, in sharing with the customer’s ideas, allows us to create highly customized robotic cells integrated with the customer’s production reality.
Arcos robotic cells are able to work pieces of any material even with very complex geometries; therefore, they are able to satisfy requests from various sectors such as Aeronautics, Automotive, Energy, Oil and Gas, Medical, Weapons, Watchmaking, Luxury and Fashion, Furniture and much more.
Replacing manual work with Arcos robotic systems is the winning choice if you have high productivity or if manual work is risky or unrewarding. The benefits obtained with these autonomous tools are manifold: production rates increase considerably, the possibility of error decreases and operators can perform more satisfying and less dangerous tasks.
Each robotized cell designed by Arcos is built with the best safety systems. In fact, each system has soundproofed and aspirated protection cabins, while the supervision of the work of the machine is entrusted to the HMI – Human Machine Interface system.
FEATURES OF OUR DEBURRING AND POLISHING CELLS
Arcos robotic systems provide the best cutting-edge technology by offering:
CASE STUDIES FOR ROBOTIC CELLS
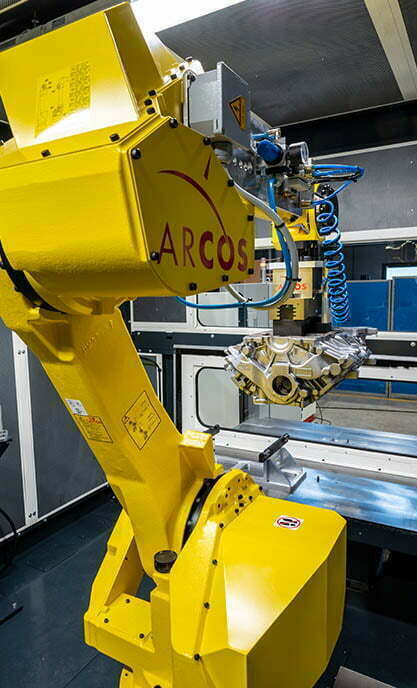
SUPERCAR ENGINE BLOCK PRECISION DEBURRING
The robotic cell is designed for the precision deburring of V8 engine blocks of luxury supercars.
Critical work points, with poor accessibility, are machined with special tools mounted on electrospindles.
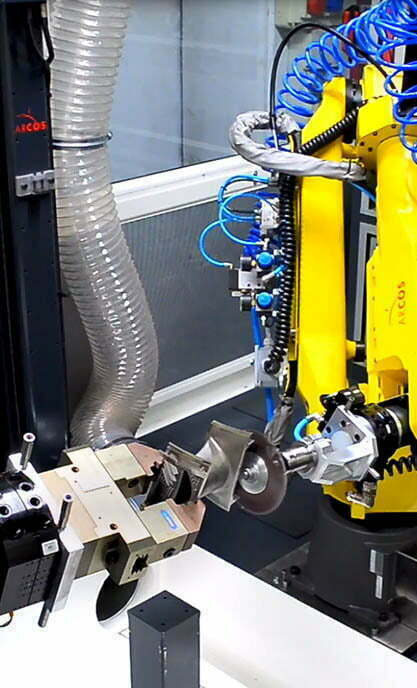
Robotic system for precision deburring of turbine blades
The Robotized System allows you to automatically remove the machining burrs, starting from micro-fused turbine blades that have different torsions.
• 2 Fanuc robots
• Automatic piece loading / unloading table
• Quick change pliers system
• Tool holder quick change system
• Magazine with 4 pneumatic grippers
• Magazine with 20 tool holder spindles
• System for the requalification and automatic repositioning of the pieces
• Vision system for piece positioning control
• RFID system for tools and pliers recognition
• 2 brushing units
• Automatic tool wear control
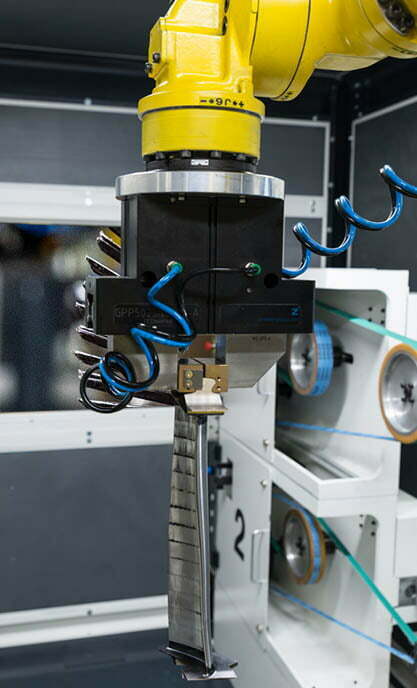
Robotic system for grinding and finishing aluminum parts for the aerospace sector
• 2 SM9 units, pendulum type unit for double brush grinding;
• 3 SB3 units, spindle unit for abrasive rubber wheels;
• 1 SM6 unit, pendular unit for abrasive belt grinding;
• 1 FANUC 50 KG robot;
• 4 automatic grippers for piece locking;
• 4 claw kit for hooking each piece;
• 1 loading / unloading system by means of a rotating table;
• 1 electrical cabinet with control panel;
• Fully enclosed protection cabin.
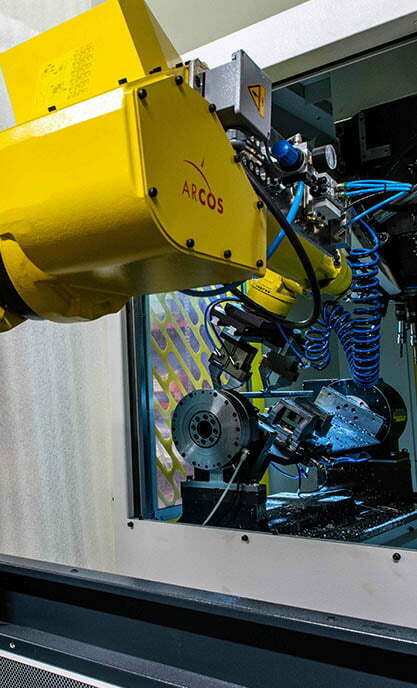
Robotized system for grinding, satin finishing and robodrill (machine tool)
• 1 six-axis robot FANUC M70Ic / 50M with DCS Fanuc safety option;
• 1 Fanuc Robodrill CNC machining center equipped with tools;
• 2 pliers for piece locking;
Loading / unloading system with rotating table;
• 1 SM6 grinding unit, pendular unit for abrasive belt grinding;
• 1 satin finishing unit, pendular unit for satin ribbon satin finishing;
• 1 double polishing unit equipped with two solid paste guns;
• 2 units for drilling / tapping;
• 1 electrical cabinet with Proface HMI control panel;
• Interface with management system;
• Communication in Profinet;
• 1 completely closed protection cabin;
Pieces: Components for sports facilities;
Material: Aluminum;
Operations: Grinding, Polishing and enslaving.
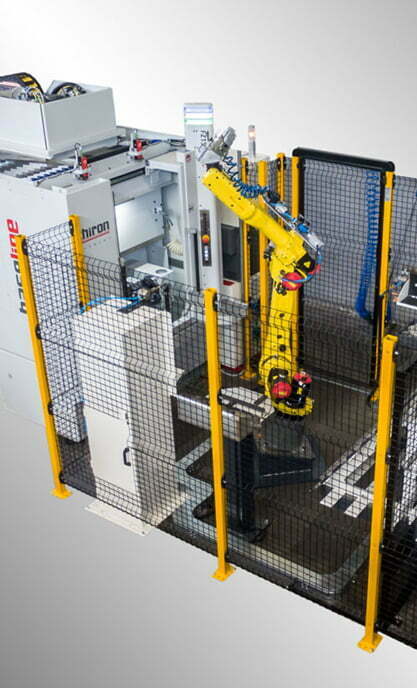
Robotized system for machine tending
• 1 six-axis robot FANUC M20iA / 20M with DCS Fanuc safety option;
• 2 double grippers for piece locking;
• Loading and unloading system with rotating table;
• 1 workpiece buffer station with piece requalification;
• Piece washing / blowing station;
• Station for piece quality control;
• Parameterized work paths generated with self-learning;
• 1 electrical cabinet with Proface HMI control panel;
• Communication in Profinet;
• Protection nets;
• Safety switch for access to the robotic island with RFID technology with integrated buttons, for command and indication
• Anti-panic system and compliant with the LOTO Lockout / Tagout procedure.
Pieces: Pneumatic and hydraulic valves
Material: Aluminum
Operations: enslavement
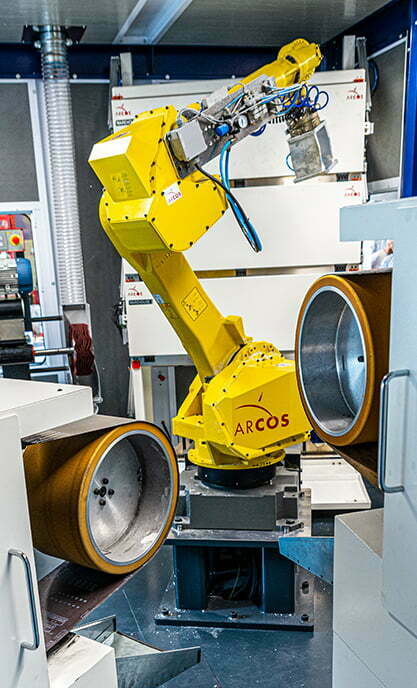
Robotic system for grinding and polishing of electrical boxes
The Robotized System allows the automatic grinding and polishing of electric boxes. The system is equipped with fully automatic component loading and unloading and a tool magazine.
• 1 six-axis robot FANUC M70Ic / 50M;
• 2 SMART double sanding units;
• 1 Double polishing unit equipped with two liquid paste guns;
• 1 Pair of mechanical / pneumatic grippers for hooking / unhooking pieces;
• 1 automatic magazine containing 25 different types of grippers;
• 1 automatic piece loading / unloading system by means of conveyor belts;
• 1 electrical cabinet with control panel;
• Fully enclosed protection cabin.
Pieces: Electrical boxes Material: Stainless steel
Operations:
• Automatic grinding by abrasive belt;
• Polishing of boxes Stainless steel.
PLEASE CONTACT US HERE TO DISCUSS YOUR PROJECT
ITALIA E WORLDWIDE
8:00 – 18:00
Via Leonardo da Vinci, 15/C 25064 Gussago (Bs) Italy
NORD AMERICA, CANADA E MESSICO
8:00 – 18:00
30 Chapin Road Suite, 1205 Pine Brook, NJ 07058 – USA